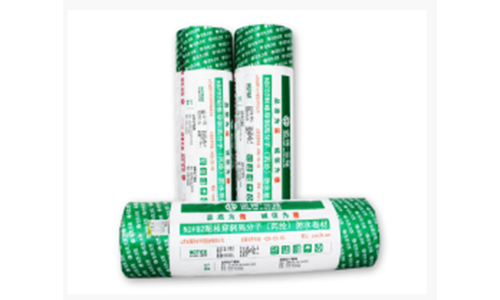
Product Overview
The full name of TPO coiled material is thermoplastic polyolefin. It was introduced into the U. S. market in the 1980s. In the early 1990s, TPO materials were applied to roof waterproof engineering by mechanical fixed paving. The material adopts special formulas, without any plasticizer and chlorine. Compared with various thermoplastic waterproof materials, it has unique low-temperature flexibility, aging resistance, stable properties and environmental protection, convenient welding, and forms a watertight whole. Therefore, TPO waterproof roll sheet have developed rapidly in the waterproof material market of industrial developed countries such as the United States and Europe.
The invention relates to a TPO waterproof coiled material, which is made of a thermoplastic polyolefin (TPO) material combined with ethylene-propylene (EP) rubber and polypropylene by an advanced polymerization technology as a base material, a polyester fiber mesh fabric as a matrix reinforcing material, and adopts an advanced processing technology to manufacture the sheet-shaped coiled waterproof material. The material has the long-term weather resistance and durability of ethylene-propylene (EP) rubber, and the weldability of polypropylene; a layer of polyester fiber fabric is sandwiched between two layers of TPO materials, so that the physical properties of the two layers of TPO materials can be enhanced, and the breaking strength, fatigue resistance and puncture resistance of the two layers of TPO materials can be improved. The TPO on the upper surface of the reinforcing layer has a high-reflectivity white light-colored smooth surface, which is favorable for environmental protection and construction safety because of no chlorine.
Product features
● TPO coiled material combines ethylene-propylene rubber and polypropylene with advanced polymerization technology, which combines excellent weatherability and durability of ethylene-propylene rubber and weldability of polypropylene.
● Special formulation technology, without adding any plasticizer that can easily make the material brittle, can have high flexibility, and will not cause the brittleness of general polyolefin material due to plasticizer migration, so as to maintain the long-term waterproof function.
● A layer of polyester fiber fabric is sandwiched in the middle to provide high tensile performance, fatigue resistance and puncture resistance of coiled materials. It is suitable for mechanically fixed roofing system.
● Excellent high and low temperature resistance, flexibility at-40°C and mechanical strength at higher temperature.
● Chemical resistance, corrosion resistance of acid, alkali, salt, animal oil, vegetable oil, and lubricating oil, and resistance of algae, mold and other microbial growth.
● Heat aging resistance and good dimensional stability.
● Light color dominated by white, with smooth surface, high reflectivity, energy-saving effect and pollution resistance.
● No chlorinated polymer or chlorine in the composition. No chlorine is released during welding and use. It is harmless to the environment and human health.
● Hot welding shall be adopted to form a high-strength sealing layer.
Scope of Application
It’s mainly applicable to industrial and civil buildings, public buildings, etc.
Various permanent key roofing waterproofing works.
Precautions for construction
● Operators must be trained for their works.
● The surface of welding material must be wiped clean without water, oil and dirt.
● Check key welding quality strictly, and there shall be no lack of welding and skip welding.
● Pay attention to the protection during the construction process. Personnel wearing spikes are not allowed to enter the construction site where TPO coiled materials have been laid.
Technical Performance Index Usage Standard GB 27789-2011
Serial No. |
Project |
Indicators |
||||
H |
L |
P |
||||
1 |
Thickness of resin layer on intermediate fabric/mm ≥ |
- |
- |
0.40 |
||
2 |
Tensile strength |
Maximum tensile force/N/cm≥ |
- |
200 |
250 |
|
Tensile strength /Mpa≥ |
12.0 |
- |
- |
|||
Elongation at maximum tension/≥ |
- |
- |
15 |
|||
Elongation at break%/≥ |
500 |
250 |
- |
|||
3 |
Size change rate of heat treatment/%≤ |
2.0 |
1.0 |
0.5 |
||
4 |
Low temperature bendability |
No cracks of-40 ℃ |
||||
5 |
Impermeability |
0.3 Mpa, water impermeability for 2 h |
||||
6 |
Impact resistance |
0.5 kg*m, water impermeability |
||||
7 |
Resistance to static load a |
- |
- |
20 kg water impermeability |
||
8 |
Joint peeling strength/(N/mm) ≥ |
4.0 or coiled material failure |
3.0 |
|||
9 |
Right-angle tear strength N/mm≥ |
60 |
- |
- |
||
10 |
Trapezoidal tear strength/N/mm≥ |
- |
250 |
450 |
||
11 |
Water absorption (70 °C, 168 h)/%≤ |
4.0 |
||||
12 |
Thermal Aging (115 °C) |
Time |
672 h |
|||
Appearance |
Free of blisters, stratifications, delamination, bonds and openings |
|||||
Maximum tensile force retention rate/%≥ |
- |
90 |
||||
Tensile strength retention rate/%≥ |
90 |
- |
- |
|||
Retention rate of elongation at maximum tensile force/%≥ |
- |
- |
90 |
|||
Retention rate of elongation at break%≥ |
90 |
90 |
- |
|||
Low temperature bendability |
No cracks of-40 ℃ |
|||||
13 |
Chemical resistance |
Appearance |
Free of blisters, stratifications, delamination, bonds and openings |
|||
Maximum tensile force retention rate/%≥ |
- |
90 |
90 |
|||
Tensile strength retention rate/%≥ |
90 |
- |
- |
|||
Retention rate of elongation at maximum tensile force/%≥ |
- |
- |
90 |
|||
Retention rate of elongation at break/%≥ |
90 |
90 |
- |
|||
Low temperature bendability |
No cracks of -40 ℃ |
|||||
14 |
Artificial climate accelerated aging |
Time |
1500 h |
|||
Appearance |
Free of blisters, stratifications, delamination, bonds and openings |
|||||
Maximum tensile force retention rate/%≥ |
- |
90 |
90 |
|||
Tensile strength retention rate/%≥ |
90 |
- |
- |
|||
Retention rate of elongation at maximum tensile force %≥ |
- |
- |
90 |
|||
Retention rate of elongation at break%≥ |
90 |
90 |
- |
|||
Low temperature bendability |
No cracks of-40 ℃ |